Sheet Metal Forming and Bending
Our Sheet Metal Bending Process
LL Potters are one of the leading providers of fabricated sheet metal products, servicing a wide range of customers across the UK, utilising the very latest in CNC sheet metal machinery and bending technology. We are able to manufacture all kinds of metal products that require forming from the simplest bracket to the most intricate of formed components or enclosures. We can meet all levels of demand from single units to batch production – so we are sure to be able to work to your exact specifications.
We offer a variety of services here at LL Potters – and one of the most in-demand of those is sheet metal forming. Our sheet metal bending machines are suitable for working with aluminium, mild steel, stainless steel, zintec and many exotic sheet materials also. We aren’t just able to guarantee the best possible results when you work with us, but we will also be able to deliver your products at a fast turnaround, all while retaining the cost-effectiveness of our sheet metal forming process. That’s why we are a firm favourite with so many customers.
Here at Potters we have several servo electric driven press brakes, providing higher productivity and increased energy saving, utilising both offline and touch screen control for fast effective programming. For small batch, fast turnaround production we can also utilise CNC automatic tool changing, massively reducing costly non productive setup procedures when it comes to sheet metal forming. This allows fast changeovers between different job batches and a one pick up operation for complex bending sequences.
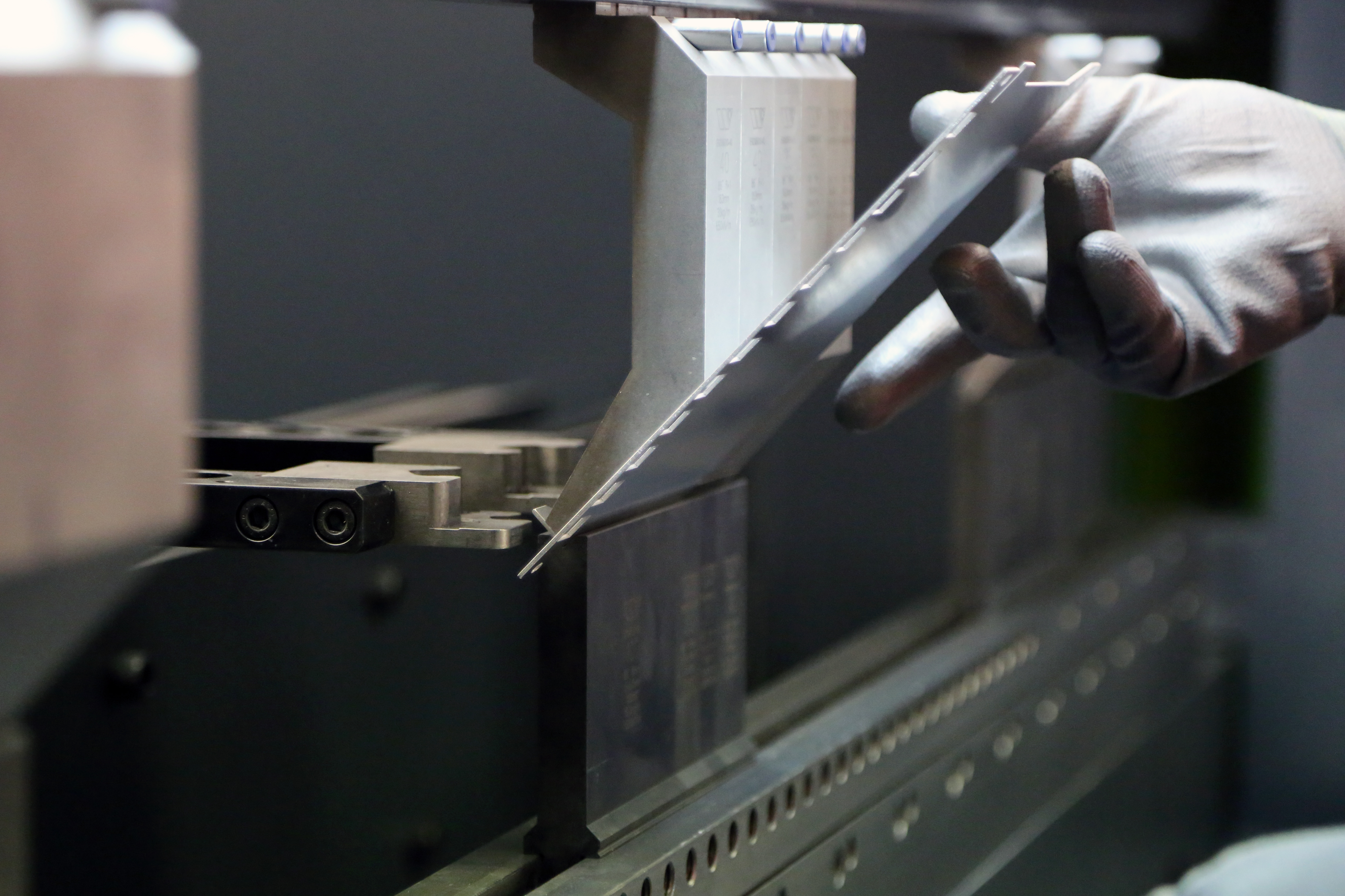
If you want to find out more, please do get in touch with a member of our team. They will be happy to answer your questions and get the ball rolling as quickly as possible.
- High accuracy and control.
- Quick tool change for speedy tool set ups.
- Automatic tool changing capabilities for small-batch, complex and prototype work
- Bespoke customer tooling available.
Forming & Bending Technical Specification:
- 7 x Press brakes (Safan/Amada)
- 1 x Amada HG1003 ATC (Auto tool changing machine)
Additional:
- Amada SPH30 power press
- Warco bending rollers
How does it work?
For those who have never used our sheet metal forming services before – how does it work? To put it simply, the bending of metal is a process whereby a force is applied to sheet metal which causes it to bend at an angle and form the desired shape. The force in question comes from a press brake. The press brake contains an upper tool called the punch and a lower tool called the die.
The sheet is placed between the two and held in place by the backstop. The bend angle is determined by the depth that the punch forces the sheet into the die. This depth is precisely controlled to achieve the desired bend.
If you want to find out more about how sheet metal forming works and if it could be right for your project, please get in touch with a member of our team today.
What should I consider when designing new sheet metal parts?
- Always try to keep the bend radius consistent, this will reduce tool changes and keep the parts more cost-effective.
- A +/- 1 degree tolerance on all bend angles is generally acceptable in the industry.
- Try to make the flange length at least 4 times the material thickness.
- Following on from the point above, the distance from the outside edge of the material to the start of a hole or cutout should be equal to the minimum flange length.
- It is recommended that the minimum inner bend radius should be at least 1 times the material thickness. This radius will vary depending on applications and material. When the radius is less than recommended, it can cause problems in some soft materials and fracturing in hard materials.
- Sheet metal parts with holes and apertures etc are fine, countersinks and tapping are all achievable in the blanking stage and can then be bent using a normal process. Counterbores and other machined features normally require an additional post process and incur additional expense.